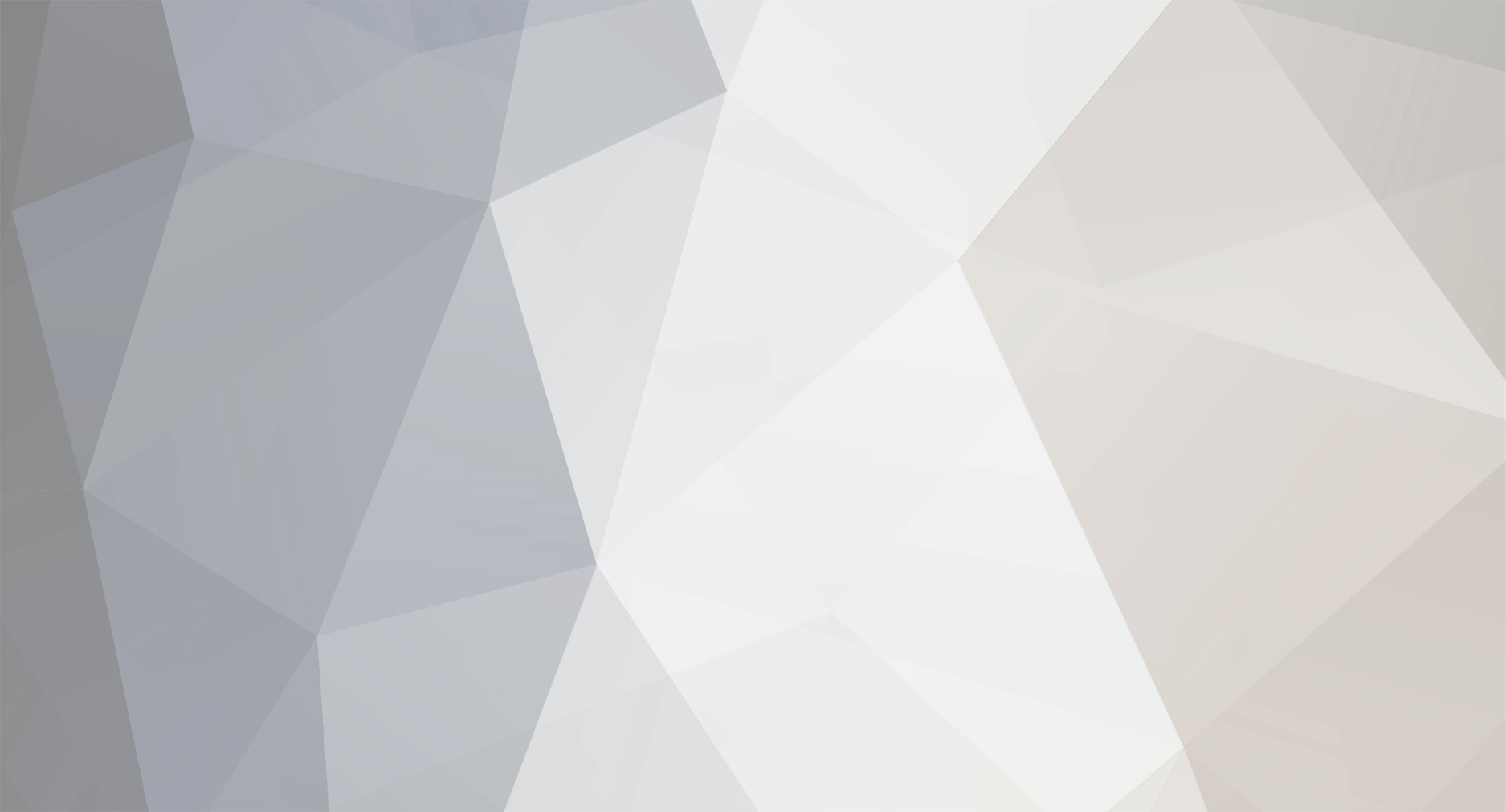
lordzogat
+Premium Members-
Posts
189 -
Joined
-
Last visited
Everything posted by lordzogat
-
I'll add my waterfall from the park in PA
-
How did you get most of your geocoins? Do you actually find them in caches, or are most of your coins from trading? What percentage? If trading is the case, did you start out by buying your own run of coin and trading from there or did you acquire a few and go from there? I looked into the cost of getting coins made and was a little turned off by the initial cost. Granted I can see why its high as your getting a quality coin, but that can be alot for some to dish out. If your willing to post your responses it will help me learn the best way to get into some ceocoin collecting or trading. I have yet to ever find a geocoin that is not a travel bug. I have been placing my Geo Tokens as a souviner for people who find the caches I frequent. I have posted in the Geocoins Trading Pinned Thread, but my tokens don't really fall under the category of geocoin. Thansk for answering the questions as it will help me where to go next. I would liek to acquire a few coins for myself and don' have any really set preferences, but have seen some really neat coins. LordZogat
-
Hey there lordzogat, Just a couple of questions, as I'm very interested in your work. Are these (shown) the token designs you are offering, or are you able to customize further? As in shape, artwork, etc. And also, can you possibly show a photo with an actual coin (or something) to gage actual size? Thanks! Yime These designs are more or less set other than changing painting scheme. As I have already developed the master tokens and formed molds from them. If you are looking for something in particualr let me know and then I can decided on the time required. The time taken to develope and mold a master token varies from 1 - 4 hours and then there is the cost fo the RTV mold rubber - so developing a new token is a possibility, just depends on what it is. The larger tokens all range around the 2 1/4" size. The small set are all poker chip sized. Hope this helps as I would love to acquire a few geo coins.
-
Hello Fellow Geocoin Owners. Alas, I have no geocoins of my own, but I have been making Geo-tokens. If anyone has multiple coins of a certain type or have some they are willing to part with, I would be more than happy to offer up a combination of tokens for your geocoin. The tokens vary in how long they take to make. The painted ones obviously take much longer. So you can place value by the labour involved. Please PM me with your offer of what token(s) of mine you want as well as a reference to your coin so I can see it. Then we can finalize up the deal from there. If you really prefer one paint scheme over another, I can make sure your token is done to your preference. NOTE: I will be changing the text color of the "Dead Set" token as it does not have the effect I am after. Thanks for looking. Note: Token F is a replica of a Plastic Pirate Coin converted into a token. H is obviously my Poker Tokens.
-
Made some better quality heavier weighted Poker chip tokens today that are numbered.
-
Printed images on labels and laminated with packing tape, applied to poker chips. I posted this in another thread, but it is really easy.
-
This is the solution I have used for coating any image for any application before its stuck to something to keep it more durable....and its CHEAP. Once the image is printed, using clear packing tape from the dollar store, carefully laminate the image. Seal the tape by running your finger nail over the entire surface (or something with a sturdy edge that is not sharp, rigid card stock folded etc etc) This helps to fuse the tape to the surface and can make it even look properly laminated. Then you cut it out and put it on your surface. It gives a sealed and high gloss finish for next to nothing. The worse part is taking your time on larger surfaces to prevent bubbles and wrinkles. I use to laminate entire board game surfaces in this manner that I created in University. They still are in great shape today 10 years later. I also use this method on my printed token labels. It also helps if your printing onto a sticker labels, then there is no need for the epoxy. Give it a shot. ------------- Here is a picture showing the process. Pinted lables, in top left, sealed lables with packing tape in top right (see the glare on them) and in the middle is the stickers applied to the poker chip sides and one cut out ready to be stuck to a token. Simple and easy once you have the graphic designed and laid out to print on the labels. I have mine alligned such that I run 3 sheets of lables through on one page of paper to print 18 circles. Poker chips are 11G to make them feel more substantial. I got them for $5 for 100
-
If you are unable to move it towards its goal or in the direction it needs to go, then the only way to log it is pick it up and put it right back in the same cache. Having said that, I would only do that if the cache you found it in, is not the cache its currently registered as being last placed. In otherwords certainly log it if you have found it in cache it is indicating it is not in. Also if the cache you have found it in, gets very little traffic or visits compared to another cache that is near by, then I would say move it to the other cache with more traffic. It may not be along the goal or direction the travel bug is asking for, but may drastically increase the bugs chances of getting moved by someone else in the right direction. Some times a slight latteral movement or movement in the wrong direction can help. If you are unsure what to do, ask the owner. But to pick it up and drop it again. loging that you found it if its where it says it already is, is pointless in my opionion. Or you could keep this in mind. Say the travel bug owner has asked for pictures along its adventure, perhaps the last person to drop it has not posted a picture at this particular location. You could grab it to take the picture and "Log your find" by posting a picture, or pick it up, go take a picture somwhere close by, then drop it back off. So there are ways around it if you really want to record it. --------------- eh, in the time it took me to write this up others replied and make very good points. I like the part of letting the owner know its still there.
-
Once I have the mold made I just use Plaster of paris to cast the tokens. Tehy then get a quick schellac bath to seal the pours and stregthen the tile ready for painting.
-
This is all very nice and I also like the home made coins but ..... the question was also "Can we get geocoin numbers for tracking them on the net ?" And hopefully, the numbers are released free of charge .... Loba2007, Quebec, Canada I believe the only option is to buy a Travel bug Tag and attach it to the item. Trackable numbers are only available at a cost of $1.50 each if they are placed on a production run of geo-coins from one of the Groundspeak approved manufacturers.
-
For the first 4 people who are willing to put up $20, I will design for you a 1.5 - 2" one sided token based on your design requests (within reason and to be approved). I will then form a rubber RTV mold and ship you the mold to use for your self to turn out any quantity of tokens you like from YOUR mold. The token is to be a single sided design. You can always paint or write more info on the back of the flat side your self. The $20 covers the design and mold. I will start with 4 first. The token can be Round, Square, Rectangle or Hexagon. The design will be as close as I can get it to your request. Lettering if placed on the mold may be restricted due to space and will be just shy of a 1/4 of an inch high. Just throwing this out there for any takes as I know lots of people have talked about wanting their own token and to be able to make lots of them. This I believe is a good offer. I have the tools and know how to make your token quickly, you simply have to buy the plaster and paint them up your self once you start making casts. I can provide hints and tips to making a good cast and also for mold maintenance. Here is a shot of some molds and their respective tokens. The larger one is actually two halves, but you get the idea. If you want to pay for more than one token, thats fine but let me know how many. ------------------------------- 3 of 4 offers still available.
-
Excellent job, are you making each one individually or making them from a mold? I read a bit further and think I just answered my own question. I did just post a tutorial on how to make your own geo token and mold to reproduce them as many times as you want. I think I saw your post there. This could save you alot of time and possibly money. A 10KG bag of quick dry plaster of paris costs me $17CND and easily makes 500 tokens. With using a mold, then most of your time is spent designing new tokens.
-
I now begin by using the dry brush method to highlight the rocks very very carefully. Last thing we want is to touch the lava pool with a dark color. I mixed some black with a silver metallic paint to make a lighter shade of black to apply to the rocks, but also used the metallic of the silver to give the rocks some shine. I then mixed a touch of black with white to make a even lighter shade to just brush over the jagged rock areas to make them stand out. In the case of this tile, there were very few layers needed to achive the desired look. In some game tiles I do, each section could have 3 - 5 base coats, 3 - 6 highlight layers on primary resource and 4 - 5 layers on secondary resources. Here is the finished tile. Here are two pictures that show the 3D features of the file from ground level. After this tile is finished its painting, I usually coat them in a flat or gloss sealer to help protect the paint. The tiles should be stored in a cool protected area and no painted surface of one tile should rest against another. I place each tile in its own bubble wrap baggie. I hope you enjoyed this tutorial and found it informative. You just have to go at it and give it a try, if you make mistakes, learn from them and push on. Feel free to comment and ask questions. Now here is one picture of all the tokens I have made for Geo Caching. The four in the top left have not yet been painted so I will update the picture when I have painted them. They are the first few from the new molds for those tokens. Lord Zogat
-
Step 15: Painting your tile. I will be using acrylic paints from any craft or dollar store. The painting process I will be using is a combination of layered painting and drybrushing. With dry brushing painting, you cover the tile in its main color in a darker shade, then you slowly add highlight layers to make the features to stand out. The dry brushing comes into play when you load a brush with a highlight color and remove the excess paint fromt he brush. Then by wiping the brush on a paper towl, we remove even more paint. When the brush is almost dry, you begin to slowly sweep the brush over the feature areas you want to highlight, and allow the paint to slowly collect on these areas. As you move the brush back and forth over the area, the more pressure you will have the apply to release more of the paint left in the brush as it is drying as you sweep the brush. We will see this process in play in a bit. Since the primary feature or resource of this tile is the lava, and since any color is transparent when compared to black, then we must do the lava painting first. Also we want lava to show up in the cracks, so the red must go first. Apply lots of red paint to the surface of the tile, again since it is very transparent paint and depending on the color being used, you may need several layers to get a nice coating. Make sure the previous layer is completely dry before going to the next layer, otherwise you just push half dried paint around, ruining your layers. Here are pictures of several layers of red being added, progressivly getting to a solid red state. I had to add roughly 4 layers to get the red color I wanted. Since the lava is warmer in the center of the pool as seen in the pictured tile, then the center is done in brighter shades of orange and yellow. You can try to blend in some orange and a touch of yellow while the last layer of red is wet, but this can be a hard and time comsuming process. It just takes practice to get a smooth blend, and going backand forth between darker and lighter shades. Always clean the brush frequently to prevent mixing of the blended colors. Time and practice, wet blending is not easy. This is often why dry brushing is better. You could also start to use the dry brush method by letting the last red layer dry completely and then start with a redish-orange dry brush highlight. Again only applying a very small amount of the shade. Continue by lightening the shades and adding a wee bit at a time. If you change the shade too quick the highlighted later stands out too much. In some cases this is wanted but not in this case for the lava temperature change. This is what too much drybrushing in too drastic of a shade change looks like. I had to step back and use the wet blend method that took alot of time to get a smooth blend. This would mainly be used for liquid surfaces only. But it depends on the look desired an application. At this point we now have the tile covered in the primary resource with its necessary high lights. We now begin painting the secondary resources and their layers. In this tile its the Black rocks that surround the lava pool. Since the black covers everything, you must take your time and use a steady hand and only cover what you want. If you make a mistake, attack that section vigerously with a wet clean brush and hope it releases the black before it has dried. This is the tile after the first layer of black is applied. Only one layer is needed. By carefully covering the rocks and their sides, I have allowed the lava inbetween the cracks to remain and stand out.
-
Step 14: Making Tiles from the cured Mold. Now that the mold has had a proper chance to set and is the right material that is spoungy and holds its shape, it is ready to make tiles. The other mold present has nothing to do with this project, but is a small building mold for another game, to be used for 3D Scenery. I put it in this picture to show you what other molds can be used for. I have poured the first tile and it has set. I removed it from the mold and filed the base flat. Now it just has to dry out for the next step The tiles have been sealed as we did with the Master Tile in step 12. This will prepare the tiles for painting which is the next setp.
-
Step 13: Preparing the Master Tile and making the mould. In this step you need to choose what type of moulding material your going to use to make your mould. There are several brands of mould making materials available and often consist of a two part epoxy mixed at 1:1 or 1:10 ratios of resin and hardner. Also you want to get a mould making material that has the right hardness factor. For moulds that flex, I would suggest a hardness shore of about 30. They cost roughly about $60USD for a 128oz kit. That was on ebay. Another method to make a mould is using a tube of Silcone Tub & Tile or Exterior Window Caulking with Mildew Resistence. It costs about $3 - $5 a tube and a tube should do 4 - 7 tiles of this size. I have found for the plaster of paris tiles I make, the silicon caulking found in tubes at any hardware store, releases the tile far better and with less damage and no releasing agent, then the mixed epoxys do. a) Using Epoxy mixed resins and hardner. Prepare the tile by covering all surfaces with vasoline and removing the excess. Place the tile in a low discardable tray about the size of the tile with a bit of room on each side. This reduces waste of your moulding compound. You may want to stick the base of the tile firmly to the bottom of the tray or surface to prevent the resin from going under the tiles flat base. For my frame I placed Packing tape on a table sureface, built a frame from lego, sealed it all with packing tape, then taped it to the surface sealing all the edges. This allowed me to customize the frame shape to the tile. Then following mixing and pouring instructions, you slowly cover the tile, degas if necessary and let it sit until it cures. Using the tube of caulking. Start by gluing a block of wood to the underside of the tile. This will act as a handle. Once dry, prepare the tile by covering all surfaces with vasoline and removing the excess. Using the silicon tube in a caulking gun, slowly push out caulking into the surface of the tile working in small areas forcing it into all the cracks. I suggest working from one area to another pushing a bit of caulking ahead of the end of the tube. This allows it to cover the tile and allows air to escape as you go, as the caulking is being pushed into the small spots instead of being droped on top and sealing air in. Once the top is covered, go and do the sides so that it just over laps around to the flat back side. Excess silicon it can always be trimed off with scissors. Place the tile somewhere such that it will stay put and untouched. I placed mine in the workshop vice. Allow it to cure for at least 12 - 24 hours or until it feels firm in all areas. The surface of the silicone will dry in a matter of hours, but the insides will take longer. The thicker the layer the longer the curing time. If you try to take it off too soon, it will tear and wreck the mould. Better to give it longer than to try to take it off too quick. The entire surface should have no squishy feel and be stiff and spongy. The thickness of the layer should be about 1/4 inch or more. There is a trade off to the thickness. The thicker it is, the firmer the mould will be and less likely it will bend out of shape from the weight of the plaster of paris, also the less forgiving the mould will be when releasing. Thinner moulds will have a tendency to with stand tearing as its flexibility is higher due to lack of firmness. Too thin and the mould will not hold its shape. Larger flatter tiles will need an equal proportion of thickness to support the bulk and mass of the tile! ----------------- UPDATE: As sometimes happens with older tubes of caulking and different types, the silcone does not cure as fast as it should. Or perhaps the enviroment in which it is in, is not suited for best curing potential. I checked the mould I did the other night, its been over 24 hours and its still squishy and the surface is tacky. This may be the caulking as it was an older opened tube that had been resealed or the temperature of the enviroment as mentioned. I will trying moving it to see how it does. This is all part of the issues you may face. I would normally use brand new tubes, but would also be making moulds for all the tiles at once, not just the one. I finally tried a new tube of Tub N Tile caulking with Mildew Resistance. It has cured and set the way I wanted. This is where making larger tiles consumes more resources in every case. -------------------
-
Step 9: Cleaning off the excess Playdoh The water will dissolve and remove the playdoh if you want, but I try to save a bit of it each time and then the rinse phase goes faster. The first picture is kind of cool the way the water is hitting the tile. This is the tile under warm water. I use regular craft paint brush to brush out the remaining playdoh as it dissolves. Step 10: Clean up and filing down the sides. Now is the time to file the edges flat. They get distorted as you make the tile, so now is the time for cleanup. You can also make some minor corrections to the details at this stage, but its all subtractive detail however. You may also need to file the base of the tile flat once they come out of the moulds. Step 11: Allowing the tile to Dry At this point the tile needs to completely dry before the sealer can be applied. Uusually this takes at least 12 - 24 hours. Oh yah, time frame - up to this step its taken about 2 - 3 hours to complete this entire process of making the tile. Maybe a bit less as I was writing this tutorial during part of it. Step 12: Sealing the tile This step should occur for both the master tile and any tiles formed from the moulds. The sealer is made from a 1:1 mix of white schellac and Methyl Hydrate. Both should be available at the hardware store. Methyl Hydrate is also used as fuel in some stoves, or used as a thinner. Mix the two together and then drop the dried tiles into the mix until air stops escaping. Drain of the excess mixture and let the tiles drip dry, then I place them in the cardboard flat from a case of pop. There is a slight odor so you may want to do this in a well ventilated location. The tiles should dry for about 24 hours, or until dry to the touch. This step prevents the britle plaster from scratching or breaking apart. It also acts to seal the pores of the material so its easier to paint.
-
Step 4: The finished tile features Here is the finished designed tile. Again its complexity and design will depend on what all you do to it and the look your going for. Think of your desired finished product. Step 5: Mixing the Tile medium In my case I am using plaster of paris. Its low cost and effective, yet can be brittle. In later steps I will show a process used to seal and harden the formed tile. Make sure you refer to the mixing guides and instructions of the medium you decide to make your tiles from. Your moulds may have to be formed from different materials to be compatible with the medium used to make the tiles. Step 6: Pouring the tile forming material Here the mixed plaster of paris is being poured into the mould slowly so as to fill all the crevasses. Depending on your medium and its behaviors you may have to pour it in a different manner, read the product specifications. Step 7: Letting the tile set. After pouring the plaster of paris to the top of the tile base, I tap the board rapidly to help any air bubbles escape tile holes and to allow the plaster to settle into all the details. Now the tile sits until it hardens. This time length depends on your medium. Quick set Plaster of Pairs is generally 15 min set time. Step 8: Removing the master tile from the Play doh Once the tile has had time to set, its time to remove the mould. The nice thing about playdoh is it comes off fast, just be careful not to damage the fragile features. First remove the bulk of the playdoh. Then using a scraping tool remove the bits around the features.
-
Apparently you can only post so many pictures per reply so i had to break this up into several posts. This tutorial was designed and based on making a 3D game piece for a board game. However the same process can be applied to making Geo-tokens of your own for very low cost. Once you have the molds made you can make as many as you need when ever you need them. For now and the sake of argument, lets assume the Magma Pool is a wierd geo token. The tile I am starting with is the Magma Pool. Step 1: Making the tile base template. Start by cutting the shape of the tile base out of corrugated card board. Layer as many as needed to get the desired thickness of the base. Then tape them together using packing tape. This holds them together as one and also provides smooth edges. Step 2: Forming the base in the modeling medium In my case I am using regular playdoh. Its forgiving but does not hold high detail and will move around as you mould the tile. If you go with a more clay like medium, you may wish to design your master in the positive. I use the playdoh as it works for what I need and allows me to release the master plaster tile easily. Press the template into the medium and get a nice set to it. Notice you will push excess medium out of the way. Use this to get a tight fit. Step 3: Designing the tile features In my case I am designing this tile in the negative. Since every feature that is added displaces the medium, for deep holes or features you may need to extract some medium first with a wire, cutting it out and leaving a hole. Then form your feature with your tools. I use several stones and bits and pieces for making my terrains. It all depends on what your designing. Remember with playdoh it moves easily so as you make features you may distort others, so you may have to extract some out of the way so it doesn't just mush around as you push it out of the way making a feature. This is the step you use your imagination with. If you can work in the negative like I do then that’s fine, but if you want really good detail, then use a sculpting medium and design your tile by removing matter. Important Note: You may want to design your tile in such a way that the mould will allow an easier release of the tile. This means none of the features of the tile should have large horizontal empty space under them between themselves and the tile base. For example, if you were trying to pour a tile that had a letter T on the base, the space under the T, would cause the mould to hold onto the T and would break the T when releasing the tile. Where as a letter L, the mould would slide right off, as there is no space under the letter that the mould holds onto. By keeping this in mind when designing the tile, when it comes out of the mould, the mould doesn't have to be stretched to release the tile, it should almost fall out on its own. This will extend the life of the mould as it will see less stretch when releasing the tile.
-
I have decided to give the badge a minit unit a try first as I managed to get one for $61 that came with 200+ buttons, so a chance to start and go from there. Will have to see how they turn out.
-
I have some in binders sealed away as well...scary
-
Cheapest way is to manufacture your own sig item. Just sit and think of some good ideas and make a prototype. I design tokens in plaster then form a mold and cast as many as needed.
-
I have looked at Badge a minit and I notice all their tools are plastic for the most part? Has this ever been an issue for you when making the buttons? Does any one else have some information on the badge a minit systems and how well they work. They are certainly cheaper than the new metal counterparts that have everything built in one unit. Thanks for the help.